In automotive manufacturing, the paint shop has historically been the most energy-intensive area of the manufacturing process, accounting for 50 to 70 percent of energy usage in automotive assembly. Much of this energy-intensity is due to the high temperature ovens needed to cure the various paint, adhesive and sealant products on a car body.
To address this, PPGdeveloped a line of electrocoat products that cure at a lower temperature and require less process time than conventional electrocoat products.
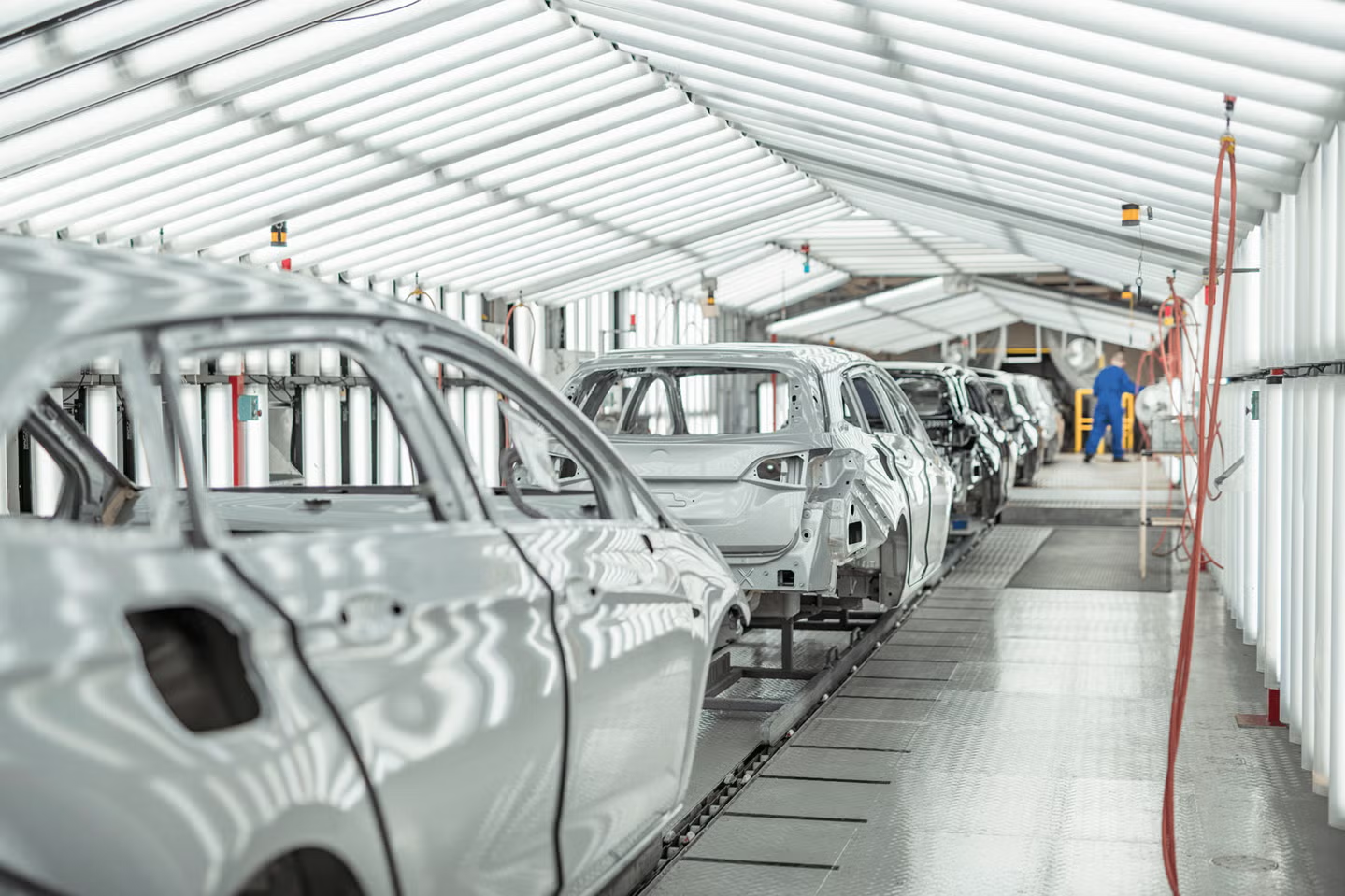
PPG’s ENVIRO-PRIME® EPIC300 expanded bake window electrocoat can be applied to heavy electric vehicle assemblies using less energy and heat, reducing the required bake temperature of the coating by 20 degrees Celsius, reducing energy input by 11 to 13 percent, and lowering GHG emissions, according to PPG. The product helps contribute to the automotive manufacturing industry’s decarbonization efforts and enables the production of battery electric vehicles without significant investment in process changes. The process is also water-based and generates minimal waste due to its application efficiency, while enhancing the corrosion resistance and appearance of automobiles, according to PPG.
In 2023, 44 percent of PPG’s total sales came from sustainably advantaged products, as defined by its internal methodology, like ENVIRO-PRIME® EPIC300. That same year, PPG partnered with a large automotive equipment manufacturer to convert its entire production lines over to ENVIRO-PRIME® EPIC coatings. Additionally, PPG has partnered with several international automotive manufacturers on the design and requirements of their new electric vehicle body designs and manufacturing processes.
PPG is working to invest in solutions to address its customers’ sustainability challenges through product innovations. The company undertakes a comprehensive methodology to designate products lines that are considered “sustainably advantaged,” as informed by the UN Sustainable Development Goals.