In the United States alone, an estimated 18.2 million mattresses are disposed of each year, with only about 19% being recycled, according to the U.S. Environmental Protection Agency (EPA). Efforts are being made by the polyurethane (PU) industry to improve the circularity of PU foams including through mechanical and advanced recycling technologies that can convert discarded materials into new products.
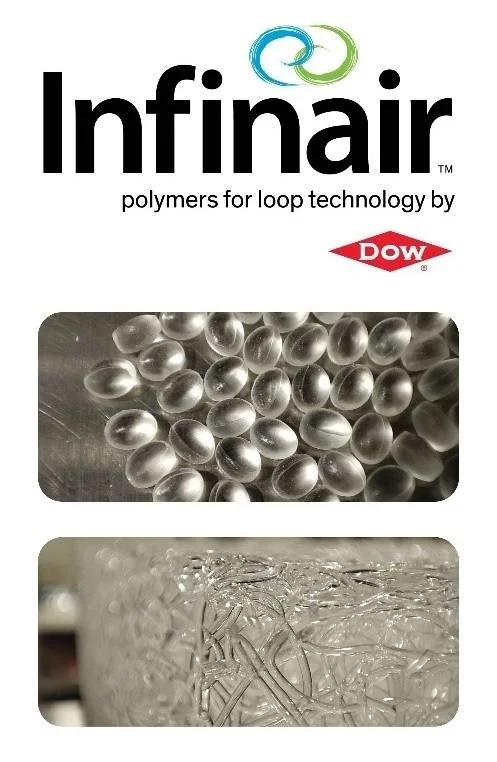
Dow’s INFINAIR™ is a sustainability solution in polyolefin elastomer (POE) technology that is used to make the randomly bonded filament loops that provide the cushion structure, which Dow describes as “3D Loop” material that can be used in a wide variety of applications, including residential mattresses, cushions and pet beds, baby pillows, medical mattresses, and outdoor furniture.
The INFINAIR™ POE solution is developed by fusing thermoplastic elastomer filaments to form thousands of bonded loops by a melt extrusion and water-cooling process.
According to Dow, the 3D Loop material made from INFINAIR™ offers better airflow, support, and comfort compared to traditional foam materials. Its 90%+ open structure and elastomeric nature embodies mattresses with many traits including high rebound and support, even body weight distribution, anti-odor and anti-bacterial properties, and more.
According to Dow, the 3D Loop material made from INFINAIR™ offers better airflow, support, and comfort compared to traditional foam materials. Its 90%+ open structure and elastomeric nature embodies mattresses with many traits including high rebound and support, even body weight distribution, anti-odor and anti-bacterial properties, and more.
Dow considers the production of INFINAIR™ POE 3D Loop to be clean, solvent-free, adhesive-free, and with little volatile organic compounds, helping to reduce the material’s carbon footprint.
INFINAIR™ POE products also show a unique advantage in carbon footprint reduction, according to Dow, because they are designed for easy mechanical recycling – in fact, the material is almost 100 percent recyclable. The material’s thermoplastic nature makes it easy to break down into material that can be used in a second life as furniture, footwear, and infrastructure like running tracks and playgrounds. It provides a new pathway to a sustainable circular economy solution by reducing around 40 percent of CO2 emissions for mattresses, according to Dow.
As part of its sustainability goals, Dow continues to create materials that can be used more efficiently and support a circular economy in applications that are designed to be recaptured, recycled and reused into the value chain.