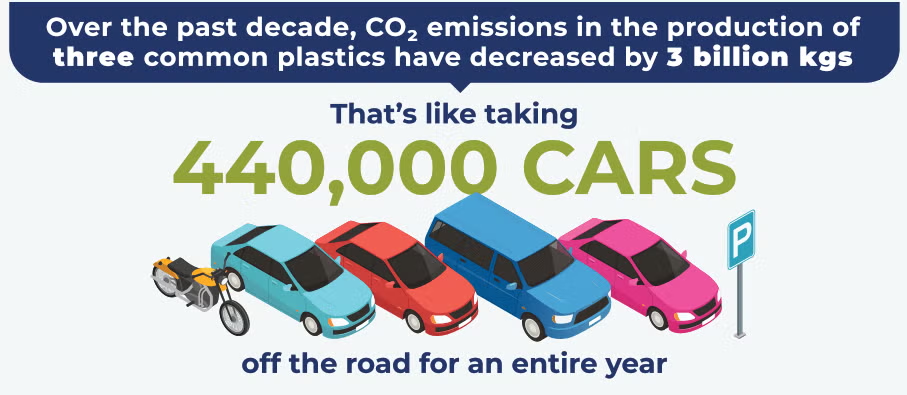
WASHINGTON, DC (December 7, 2023) – A new report, spanning data from 2005 to 2017, delves into the remarkable decline in greenhouse gas emissions (GHGs) and energy consumption during the production of plastic resins. The plastics manufacturing industry showed a significant reduction in global warming potential even while consumers and businesses demanded the material for cars and trucks, new homes, packaged goods, and other products that rely on plastics. A new report, “A Decreasing Footprint: A Review of Resin Life Cycle Assessments,” the second in a series of three of life cycle assessment reviews, looks at trio of thermoplastics (HIPS, GPPS and ABS) commonly used in automotive, construction, protective packaging and household items.
The report showed that over the past decade:
- The environmental footprint from the production of three common thermoplastics shrank, as measured by GHGs and energy use, as well as the associated global warming potential (GWP). The GHGs from the production decreased notably – by 13% per kilogram of resin produced. The emission reductions are equivalent to removing 440,000 cars from our roads for one year. That’s the same amount of GHGs as all car owners in Delaware not driving for a year.
- The positive trend toward lower GHGs is expected to continue as production shifts to lower carbon fuel sources, including renewables.
- The positive trend toward lower energy use is expected to continue due to efficiency improvements in the production of resins and their precursors.
- The first report in this series, which focused on LDPE, LLDPE, HDPE and PP, found even more promising data, with the production of those four plastics increasing over the same time period while associated GHGs decreased significantly – by the equivalent of removing 1 million cars from our roads for one year.
“Plastics offer a one-two punch as we transition to a lower carbon future,” said Ross Eisenberg, president of America’s Plastic Makers®. “Plastic products are often found to have lower lifecycle greenhouse gas emissions compared to many common alternatives."
Resins Included in the Report
These three durable thermoplastics find widespread application across various sectors, notably recognized for their significant contribution to human safety. They are used in everyday goods ranging from bicycle helmets to automotive body parts, helping to reduce injuries and keep passengers safe.
- High impact polystyrene (HIPS) – produced from a combination of polystyrene and rubber, making it more impact resistant, is commonly found in appliance parts, automotive, computer housing, toys and food packaging. There was an 11 percent reduction of GWP in the production of HIPS over the past decade.
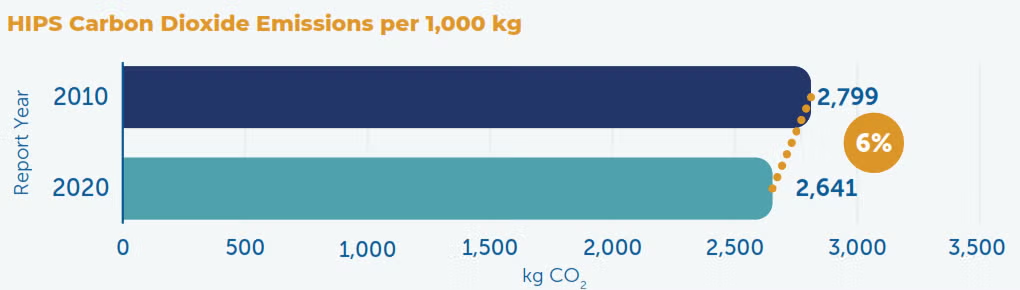
- General purpose polystyrene (GPPS) – a transparent polymer known for its glass-like clarity is typically used for protective packaging, bottles and food containers, as well as commonly used household items like toothbrushes, pens and children’s toys. From 2010 to 2020, there was a 10 percent reduction of GWP in the production of GPPS.

- Acrylonitrile butadiene styrene (ABS) – highly durable, well known in children’s toy bricks, and commonly used in protective headgear (helmets), automotive components, kitchen appliances, and musical instruments. A remarkable 24 percent reduction of GWP was made in the production of ABS.
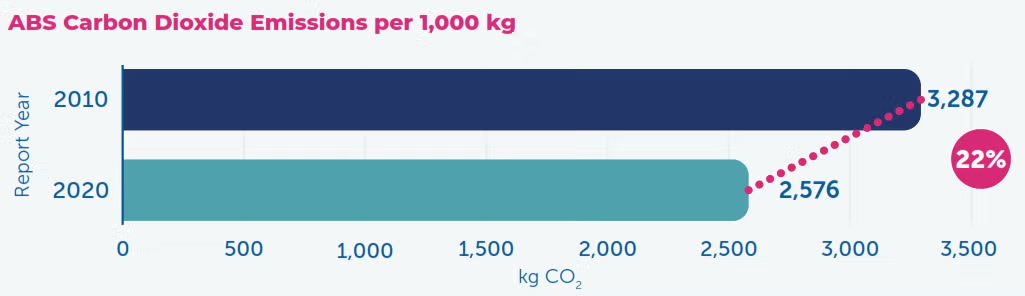
The LCAs, conducted by Franklin Associates in 2010 and 2020, began with the extraction of raw materials and ended with the plastic material (or resin) or resin precursor leaving the manufacturing facility, typically called a “cradle-to-gate” LCA. The studies looked at the environmental footprint of multiple types of plastics, using data from 2005 and 2017, respectively.
The data from this report are available in the U.S. Lifecycle Inventory Database, and the full studies are available on ACC’s website. This information can help inform decision-making related to the environmental footprint of materials over their full lifecycles.