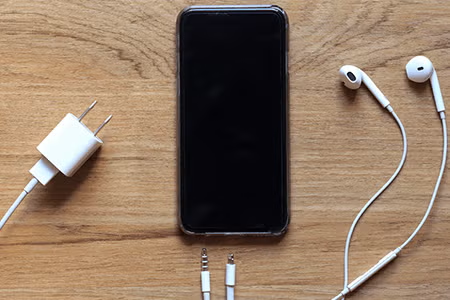
In modern times, electronic products, from smart phones to television sets to kitchen appliances and much more, have become ubiquitous in our everyday lives. However, the expansion in functionality, and rise in popularity that these electronics enjoy, has been matched with an increased need to achieve optimal performance while ensuring each product meets strict safety codes and standards, particularly around the potential for spark and fire outbreaks.
Organohalogen flame retardant (OFR) chemistries, which have been added to component materials used in the manufacture of household products for more than 50 years, are a critical tool helping to achieve these standards by making materials less likely to ignite and delaying the onset of combustion that still may occur, slowing the spread of any subsequent fire. Overall, these chemistries offer a versatile, cost-effective, and widely accepted solution to help enable safe use of electronics, improve the material stability and thermal management of these products, and provide highly effective electrical insulation.
There is a movement afoot, however, to ban or restrict OFR chemistries in favor of often vaguely described “alternatives” that may not provide the same level of fire protection, material compatibility, and cost-efficiency. Proposed regulatory mandates for use of alternatives could lead to severe economic challenges, supply chain disruptions, code and compliance conflicts, and compromised fire safety of these products.
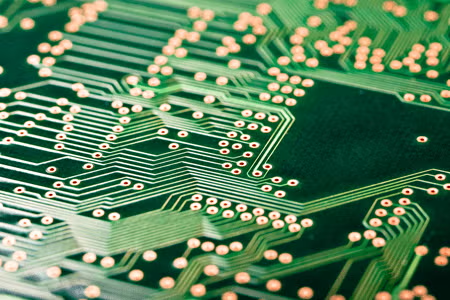
This challenge is particularly grave for electronic products due to the high density of electric components and combustible materials such as plastics. In addition, OFR chemistries applied to the components and materials of each of these products are just one of potentially hundreds or thousands of different substances and materials that must all work together seamlessly. OFRs have a long and successful legacy of application in the electronics industry and have been optimized for their health profiles, fire protection performance, and compatibility for product design.
For a real-world perspective, Tim Cassidy spent more than 10 years as director of product compliance and safety for a large consumer electronics retailer and led oversight of the company’s product safety programs including compliance with product safety standards.
"In theory, it's fine to encourage the use of alternative flame retardants – if they are as effective, safe, and available, but you have to understand the entire business of manufacturing, with extremely complicated supply chains that are interconnected, well-established, and have very long lead times. If these alternative materials are available in the necessary volumes required for industry, and that’s a big ‘if’, will they [cost] to acquire? How will the product’s supply chain be affected?"
Cassidy also pointed out that for product manufacturers, fire resistance is just one of many properties they must take into consideration, alongside resistance to impact, shock, corrosion, moisture, and more, and flame retardant additives have demonstrated they do not clash with chemistries used for those other purposes.
“Remember that FRs are a component among all sorts of other substances utilized to make a product, and we now know from a long history of use that OFRs mix well with these other substances. Will alternatives simply fit neatly into the gap if legacy OFR chemicals are not used? What process changes would be required? And do these alternatives meet the regulatory safety requirements that FRs have met for many years?”
He also pointed out that not only must OFRs and any potential alternatives work in concert with other chemistries within a product, they must also be adaptable to the manufacturing environment and equipment used to produce it. “Just because some alternative works in a lab does not mean it works in a full-scale production context. There may be alternatives but they’re not necessarily ‘moldable’ in the way that plastic products require. These massive molding machines are extraordinarily complex and are designed to operate with the current plastics and chemistries in use today. You change the plastic composition, you change the whole outcome. So when they say there’s these alternatives available, that does not mean the facility’s equipment can accept the material.”
Ultimately, Cassidy said he understands that concerns about potential health effects from OFRs should be considered, but he adds that there should be a wider perspective on the issue including product design and fire safety benefits. Cassidy also pointed out that those advocating for alternatives mandates often fail to distinguish between FR applications on surfaces that receive frequent human contact (touch screens, outer casings, knobs and buttons) and surfaces that are rarely touched or externally exposed (circuit boards, wiring casings, and other internal machinery).
“When I’ve heard people talk about the possibility of health threats that may or may not arise from OFRs, I try to point out the very real and proven health threats that come from fire,” he said. “Fire is dangerous. You can die from inhaling it, touching it, it’s acute, it’s rapid, it’s dangerous, it spreads, and it’s deadly. So from my perspective, fire is the real threat, and flame retardants significantly reduce that threat by a wide margin.”